Why use zircon bricks for the construction of glass kilns? In the glass melting furnace, the molten glass liquid and the flame-flying material will cause certain erosion and damage to the zircon refractory bricks. refractory lining of the kiln, which in turn affects the service life of the glass-melting furnace. In addition, it is necessary to reduce the pollution of the molten glass.
Zircon Bricks for the Construction of Glass Kiln
From the performance indexes of representative zircon bricks for glass kilns at home and abroad, zircon bricks are more wear-resistant, more resistant to corrosion, and can reduce the pollution of molten glass. Zircon brick with such properties for glass kiln:1. High refractoriness and high softening temperature.2. anti-slag liquid erosion ability, strong acid resistance.3. High compressive strength.4. Good thermal shock resistance. The zircon brick is used for the working layer of the glass kiln wall, and its density is high, and it is strong against the glass liquid as the working layer of the pool wall. Therefore, the choice of zircon brick refractories for glass furnaces can extend the life of glass furnaces and improve the quality of glass. The zircon bricks used in the glass kiln are made of zircon as the main raw material, added with a binder and an additive, and are equipped in proportion, stirred, kneaded, formed, dried, and then fired at a high temperature. Zircon bricks with the zircon castables can work better in the glass kiln.
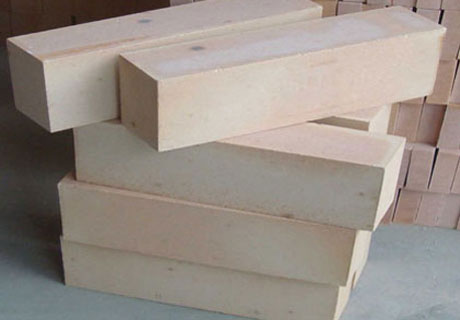
What is the price of zircon bricks for a glass kiln? The price of zircon bricks on the market is currently not fixed. The actual price of zircon bricks for a glass kiln needs to consult the manufacturer, combined with the actual situation of the glass kiln, in order to get the most satisfactory products and quotations.
Performance of Sintered Zircon Brick for Glass Kilns
High temperature-resistant and corrosion-resistant zircon bricks are made of zircon as the main raw material, added with binders and additives, equipped in proportion, and fired at high temperature after mixing, mixing, molding, and drying. Also called sintered zircon brick.
Zircon bricks are divided into the high-density type and dense type according to production technology and physical and chemical indicators. RS Company Zircon Refractory Bricks for Sale, Sintered Zircon Brick for Glass Kilns, and Sintered Zircon Bricks for Glass Kilns are mainly used for the working layer of the wall of the glass kiln. Its density is high, and as a working layer of the pool wall, it has a strong ability to resist the corrosion of glass liquid. In recent years, the world’s glass industry melting furnaces have developed in the direction of large-scale and energy-saving.
Dense Zircon Brick with High Density and Low Porosity for Glass Kiln
The dense zircon brick with high density and low porosity is a special type suitable for the lining of the glass furnace melting pool for glass fiber melting. Generally, the production method of whole powder material, casting molding, and high-temperature firing are adopted. Performance of Dense Zircon Brick for Glass Kilns. 1. High refractoriness and high softening temperature. 2. Strong resistance to slag liquid erosion and strong acid resistance. 3. High compressive strength. 4. Good thermal shock resistance. Zircon Brick for Glass KilnsMethod for Improving Performance of Sintered Zircon Brick for Glass KilnsZircon bricks have high refractoriness and load softening point, low thermal expansion rate, and are not easily dissolved by chemical attack of molten slag. However its resistance to penetration (infiltration resistance) is poor, and the slag can penetrate into the brick through the pores. At the same time, it reacts with the decomposed zircon particles to form a metamorphic layer and collapse the brick structure. To improve the use effect of zircon bricks, the permeability of its slag must be reduced.
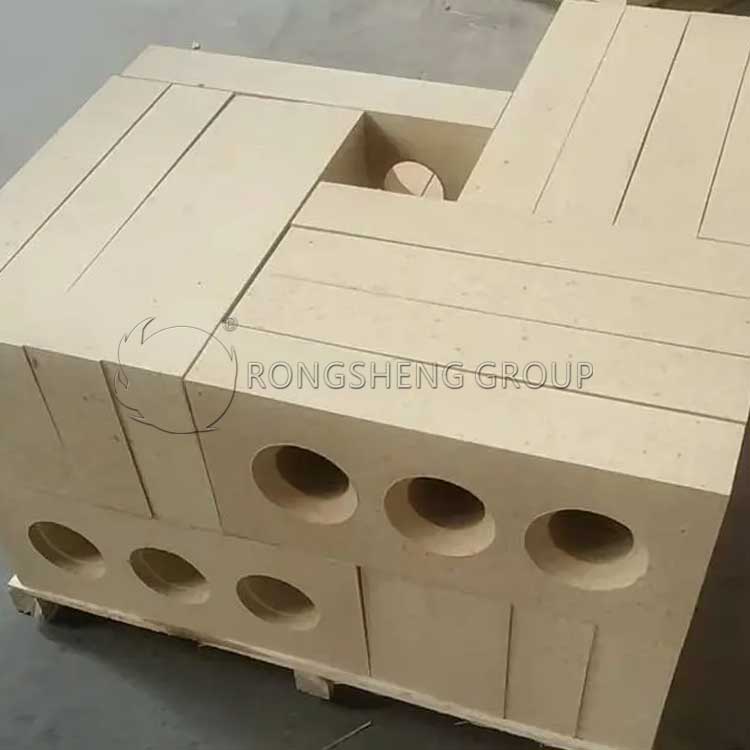
The improvement method is as follows: ① By adjusting the particle composition and changing the molding method, products with low porosity and air permeability are produced. However, products made by this method will inevitably reduce their thermal shock stability.②Add some additives to the bricks to increase the viscosity of the bricks and molten slag. High-purity zircon raw materials, a small number of high-efficiency additives, and suitable firing temperatures are the key factors for making high-density zircon bricks. The introduction of additives can not only ensure that the product can be fully sintered at a temperature far lower than the decomposition temperature of zircon but also reduce the reactivity, wettability, and permeability between the molten glass and the brick to varying degrees. Clay combined with zircon bricks, the type and amount of clay used greatly affect the properties of the bricks. The addition of clay will reduce the refractoriness of the product because Al2O3 has a solvent effect on zircon. In the ZrO2-Al2O3-SiO2 ternary system, when the composition is ZrSiO4 15%, Al2O3 15%, and SiO2 70%, a eutectic liquid phase is formed, and its melting point is 1610℃.
As the firing temperature increases, the apparent porosity of the clay-combined zirconite brick decreases, the air permeability increases, the number of coarse pores increases, the compressive strength and high-temperature flexural strength increase, and the corrosion resistance of the product increases. At the same time, the thickness of the impregnated layer increases. When the binding clay is not added, the proportion of the fine zircon powder is changed, and the test result of sintering at 1500 ℃ shows. As the amount of zircon fine powder increases, the air permeability decreases, the number of fine pores increases, and the corrosion resistance of the product becomes better. When the amount of zircon fine powder is 60%, the thickness of the impregnated layer is the thinnest. It can be seen from the above analysis that to adjust the corrosion resistance of the product, reduce the air permeability, improve the pore distribution, and obtain a zircon product with strong resistance to penetration. In the process, it is necessary to consider adopting a suitable firing temperature, adding an appropriate amount of fine zircon powder, and using a small amount of bonding clay.
For more information about zircon bricks for glass kilns, you can send us an email or by WhatsApp: +86 185 3831 2977.