Due to the unstable factors of the converter operation, some parts of the furnace lining will be damaged prematurely. At this time, the converter lining needs to be repaired, and the repair should be maintained until the life of the lining is terminated. Repairing the furnace lining is beneficial to balance the damage of the furnace lining, reduce production costs, and extend its service life. In the later period of use of the furnace lining, the number of repairs continued to increase, and the repair time continued to extend. If the stable operation of the converter has been affected, the life of the furnace lining has also come to an end at this time. In the consumption of refractory materials for the entire furnace lining, the reasonable amount of repairing refractory materials is 1/3-1/2. The repair methods of lining refractories can be divided into two types: the “feeding” repair method and the gunning repair method. Next, Rongsheng refractory manufacturers will introduce the two Repair Methods and Required Refractory Materials of Converter Lining.
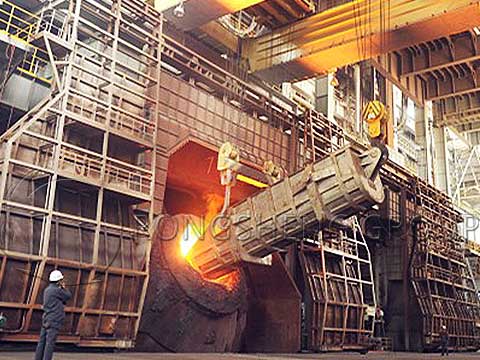
Refractory Materials for the “Feeding” Repair Method
Put the filling material into the furnace from the furnace mouth, and shake the furnace body. The residual heat in the furnace makes the feeding material have a certain fluidity, and the feeding material is spread on the damaged part of the furnace lining. Refractory materials for the “feeding” repair method shall have the following characteristics:
- (1) At the waste heat temperature of the converter lining (800-1200°C), the refractory for refilling should have good spreadability.
- (2) The refractory material for the “feeding” repair method should be cured quickly after spreading.
- (3) The solidified dosing material has good adhesion to the original furnace lining material.
- (4) The feeding material itself should have good corrosion resistance.
The basic raw materials of refractory materials for the “feeding” repair method are magnesia sand and magnesia dolomite sand, and their performance mainly depends on the binder. Commonly used binders are resins, asphalt, and their mixtures. Asphalt is cheap and easy to use, so my country’s iron and steel enterprises favor the use of asphalt-combined refractory materials for the “feeding” repair method.
Refractory for Gunning Repair Method
When the partial part of the converter lining (such as the trunnion) is damaged, the refractory material can be sprayed to the part, and the refractory material and the lining brick can be sintered together, so as to achieve the purpose of repairing the furnace lining. Gunning methods are mainly divided into three types: wet method, semi-dry method and flame method. At present, most domestic and foreign steel companies adopt semi-dry gunning technology.
(1) Wet gunning. The wet gunning refractory is mainly made of magnesia, which is put into the gunning tank, mixed with an appropriate amount of water, and sprayed to the corroded part of the furnace lining, and the thickness of the gunning layer is 20-30mm. This method is easy to use, and it can be used 3 times in one shot.
(2) Semi-dry gunning. The gunning machine used in semi-dry gunning is composed of a storage tank, a compressed air transport mechanism, and a nozzle. The gunning refractory material in the storage tank is fed into the nozzle by compressed air, mixed with 10%-18% moisture, and sprayed on the working surface of the furnace lining at a certain speed under air pressure, and the gunning refractory material is bonded and solidified. The factors that affect the gunning effect include the following two aspects.
- ①Temperature. Furnace lining gunning is carried out in a hot state, and the residual temperature of the working face significantly affects the gunning effect. The suitable temperature is 800-1000°C.
- ②The particle composition, binder, water addition and air pressure of gunning refractory materials. The gunning material is magnesia or magnesia dolomite with a particle size of less than 0.1mm. The binding agent is powdered sodium silicate, sodium phosphate, calcium and potassium phosphate and chromate. Adding a bonding agent can increase the adhesion of the gunning material so that it can be effectively attached to the working surface of the furnace lining. At the same time, the binder can form a high-temperature mineral phase at high temperatures. This not only makes the gunning material and the lining working surface firmly sintered together, but also makes it own good corrosion resistance.
The adhesion rate of gunning refractories is generally greater than 85%, and the number of uses is 3-5 times.
Semi-dry gunning is a simple and feasible method to repair converter lining. However, in the gunning process, due to the residual heat, when the added moisture contacts the repaired working surface, a large amount of steam will be generated and a certain vapor pressure will be accumulated, which is not conducive to the bonding of the gunning refractory and the working surface.
(3) Flame method. Flame gunning does not add moisture, but add combustible materials (such as coke powder, coal powder), combustible gases (such as propane, methane, oxygen). Gunning refractory materials burn and generate heat during the injection process, and part of the materials become molten. When they come into contact with the high-temperature working surface, they will quickly melt and sinter together. Flame gunning is usually carried out in the working gap after the converter is tapped. The gunning time is very short, the residual temperature of the furnace lining is high, and the adhesion effect is good. The service life is also longer, generally 10-20 times of use.
Rongsheng refractories manufacturers have rich experience in the production and sales of refractories. We can provide the most suitable refractory materials for the construction and repair of refractory linings of various industrial kilns, as well as the design of refractory materials for refractory linings of various industrial kilns. If you have questions about refractory lining materials for industrial kilns, please contact us. We will provide you with the most suitable solution for kiln production needs.