Carbon black is mainly an aggregate of approximately spherical particles of elemental carbon melted and combined. Today, it is mainly produced by oil furnace process, which can produce carbon black of different varieties and different particle sizes.
Brief Introduction of Carbon Black Production Process
Most of the production of carbon black uses an oil furnace. Usually, the oil furnace process uses a cylindrical reactor similar to a large oil burner, which consists of 4 zones (or chambers), namely the combustion zone (chamber), throttling ring (chamber), reaction zone (chamber), and quenching zone (chamber).
The preheated air and the burning raw materials added in the combustion zone provide the high temperature required for the production process, and it is also the starting point of the channel for the raw materials to enter the reaction zone. The throttling ring separates the combustion zone and the reaction zone, and at the same time increases the gas velocity entering the reaction zone. The reaction zone forms carbon black, and the particle size, shape, and hardness of the carbon black are controlled by temperature, gas velocity, and different “seed” materials introduced with the raw materials.
The quenching zone uses water to sharply reduce the temperature, thereby ending the reaction in the furnace. The operating temperature varies during the entire reaction process of the reactor. The heating operation starts from the front end of the combustion zone, and the temperature increases towards the throttling ring. The temperature is highest and the speed is fastest at the throttling ring. In the reaction zone, the temperature drops slightly, and the speed becomes quite slow. The reaction time is changed by spraying cooling water at different positions along the cooling zone, that is, the temperature is lowered by rapid water spraying.
In addition, when the type of carbon black changes, there will usually be drastic temperature fluctuations. When the position of the cooling zone changes, it will also cause a sharp change in temperature. Such a sharp temperature change will cause the refractory bricks to peel off and be damaged. The size of carbon black particles is limited by the size, structure, temperature of the furnace and the length of time they stay in the reaction zone before cooling. The bottom operating temperature and the position of the first water spray depend on the grade of carbon black.
Selection of Refractory Materials for Reactors
The most ideal refractory materials for carbon black reactors should have the advantages of high refractoriness, good thermal shock stability, high density, low porosity, high temperature corrosion resistance, and strong erosion. Most carbon black reactor linings are built with Al2O3-SiO2 refractory bricks, among which high alumina bricks or clay refractory bricks are used for the lining. Different grades of refractory materials need to be used for lining when the operating temperature range is different. The lining of the reactor operating in the low temperature range (1550-1750℃) is generally built with mullite corundum bricks. Sometimes high-purity high-alumina bricks are used for the cooling zone.
The lining of the reactor operating in the high temperature range (1750-1925℃) is usually built in sections. On the hot surface of the combustion zone, 90% A1203-10% SiO2 refractory bricks are generally used for lining. In the high-temperature throttling ring and the hot surface of the reactor, 99% A1203 corundum bricks and chrome corundum bricks with good thermal shock resistance are used for masonry. In the ultra-high temperature range (greater than 1925℃, i.e. 2000-2100℃), zirconium chrome bricks are used for masonry.
(1) Al2O3-SiO2 refractory materials.
In the SiO2-Al2O3 series of refractory materials, when W (Al2O3)>90%, it is called corundum brick. When pure SiO2 and Al2O3 materials are used to produce corundum bricks, the temperature at which the liquid phase appears is 1840℃. The physical properties and performance of corundum bricks produced by traditional processes cannot reach a very ideal level, and their thermal shock resistance is poor. Now, by using pure raw materials and in-situ forming bonding technology, the physical properties and performance of corundum have been greatly improved, and the variety is increasing. Among them, the original mullite combined with 90% Al2O3 corundum bricks and special Al2O3, combined with 94% Al2O3, and even 98% Al2O3 corundum bricks have been developed one after another.
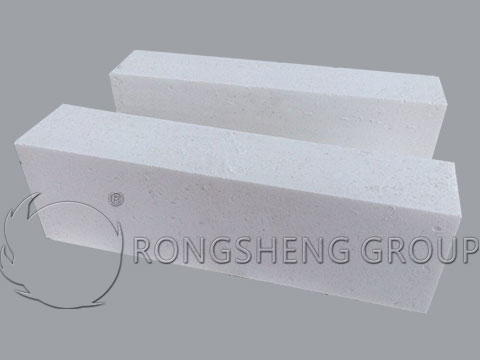
These special corundum refractory bricks have lower porosity, higher density, greater strength, and outstanding thermal shock resistance than traditional corundum refractory bricks of the same material. The 50mm×50mm×76mm sample was kept at 1200℃ for 10min, water cooled for 2min, and placed in the air to dry for 8min as one cycle, which was more than 40 times. The traditional refractory bricks are only 2-7 times, and even the traditional mullite corundum bricks are only 10-15 times. Special mullite combined with corundum bricks are mainly used in low-temperature carbon black reactors, or in the cooling zone of high-temperature carbon black reactors. The actual use structure shows that when used in the combustion and restriction zones, the special mullite combined with 90% Al2O3 combined corundum bricks (95%-98% Al2O3) are mainly used in the reaction zone with harsh conditions in the carbon black reactor, and its use temperature limit can reach 2000℃.
(2) Al2O3-Cr2O3 refractory materials
a. Al2O3-Cr2O3 materials used above 1800℃
In order to be suitable for the lining of the combustion chamber and other parts of the carbon black reactor with a temperature exceeding 1800℃, and to have good corrosion resistance and high thermal shock resistance. The usual practice is to add a certain amount of industrial Cr2O3 powder to the corundum brick to improve its high-temperature performance.
Its high temperature flexural strength increases with the increase of Cr2O3 content. The research results show that the thermal shock resistance and wear resistance of this type of refractory brick are also improved with the increase of Cr2O3 content.
When Al2O3-Cr2O3 (10% Cr2O3) refractory castables are used as the working lining of the combustion chamber, throat, and reaction section of the carbon black reactor that are not in contact with high-temperature gas, it can ensure the safe operation of the carbon black reactor under operating conditions above 1800℃.
b. Cr2O3-Al2O3 materials used under ultra-high temperature conditions
Under the condition of temperature exceeding 1925℃, i.e. 2000-2100℃, corundum bricks are no longer competent. For example, the operating temperature of the hard carbon black reaction furnace used to manufacture low rolling friction tires is as high as 2100℃. Under such conditions, it is necessary to develop better quality refractory bricks to adapt to the ultra-high temperature conditions.
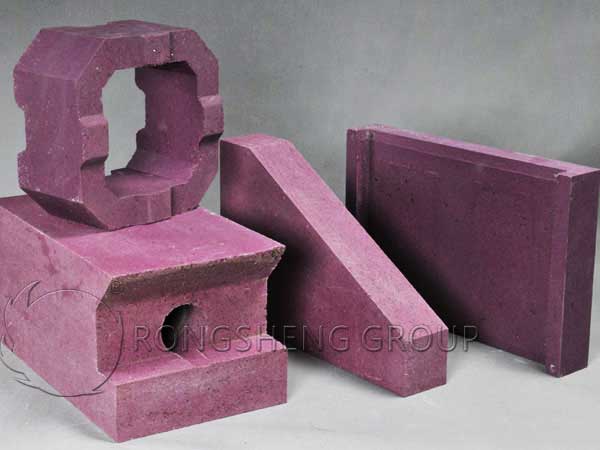
Research and development of performance requirements for lining refractory materials used under ultra-high temperature conditions of carbon black reactors:
- ① High refractoriness to avoid melting and allow higher operating temperatures;
- ② Good thermal shock stability to reduce cracking and spalling damage;
- ③ Low porosity (high density) to improve corrosion/erosion resistance.
Based on the research results of carbon black lining refractory bricks and the existing experience of using chrome alumina corundum bricks under high temperature conditions (1750-1925℃), the lining refractory bricks for carbon black reactors used under ultra-high temperature conditions should be selected from the Cr2O3-Al2O3 system.
When chrome corundum bricks with high Cr2O3 content are used as refractory materials for the lining of carbon black reactors, the service life can be extended under high temperature operating conditions. The normal operation of the reactor can also be ensured under ultra-high temperature operating conditions. In addition, the actual use results show that the service life is extended when the flow limiting chamber using high-temperature ash or high-vanadium combustion oil and the flow limiting chamber caused by intermittent high temperature melting are using Cr2O3-Al2O3 refractory bricks with high Cr2O3 content combined by solid solution. And the operating temperature in the carbon black reactor can be increased by 150-170℃ compared with the previous limit temperature.
Usually, because chrome corundum bricks with high Cr2O3 content are very expensive, they are only used in carbon black reactors operating at about 2100℃ (i.e., generating hard carbon black), and a comprehensive masonry scheme is adopted. That is, using 70% Cr2O3 and 25% Al2O3 refractory bricks to build the highest temperature, and using 20% Cr2O3 and 25% Al2O3 bricks to build the low temperature, better results can be obtained.
(3) ZrO2 refractory materials
Pure ZrO2 is extracted from zirconium-containing ores. High-purity ZrO2 is white powder with a high melting point and high density. Its mullite hardness is 6.5, its thermal conductivity is low, and its thermal expansion coefficient is large (25-1500℃, α=9.4×10-6/℃). Moreover, it has a weak relationship with temperature and good chemical stability. The high-temperature vapor pressure at 2000-2300℃ is very low, the evaporation rate is not high, and the decomposition pressure is also low. Therefore, ZrO2 refractory materials are an important type of refractory bricks for high-temperature furnace linings.
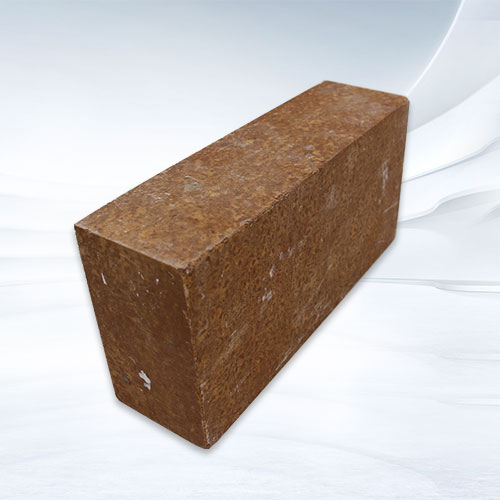
(4) High-purity MgO bricks
High-purity magnesia bricks are structural materials for high-temperature furnace linings, and their operating temperature can reach 2200°C. However, under such conditions, such as when used in ultra-high temperature environments in carbon black reactors, the purity and performance of high-purity magnesia bricks need to be carefully balanced.
Refractory bricks (including magnesia bricks) are not only resistant to high temperatures and corrosion (erosion), but must also be as stable as possible during use. It is generally believed that the purity of magnesia and the porosity and periclase grain size in terms of physical properties are key parameters for improving the service life of high-purity magnesia bricks.
The MgO content in magnesia is an important indicator of magnesia quality, but the MgO content alone is not enough as an evaluation criterion. The relative content of impurities, especially those that easily form melts under high temperature conditions, is also important. Among the impurity components, B2O3 and SiO2 are the first, followed by A12O3, Fe2O3, MnO and CaO. Their influence depends not only on their content, but also on the Ca0/SiO2 ratio to evaluate the influence of each component on the quality of magnesia sand. It is usually hoped that the magnesia sand has a high CaO and SiO2 ratio in order to obtain the best high-temperature performance.
Magnesia bricks used in ultra-high temperature environments require high purity because high-purity magnesia bricks have high temperature strength. The high temperature flexural strength of magnesia bricks tends to decrease slowly with the MgO content from 90% to 98%, but when the MgO content exceeds 98%, it suddenly increases. When the MgO content increases to more than 99%, its high temperature strength can be significantly improved. In this case, the influence of impurity types has become insignificant. Because, in this case, the impurities exist in isolation at the junction (corner) of periclase grains. Therefore, the MgO-MgO direct bonding organization is well developed, the high temperature strength is large, the material has high wear resistance, and strong corrosion (erosion) resistance.