At present, most of the iron troughs of large blast furnaces use vibrating castables, which have many disadvantages due to the influence of many factors. For example, due to the influence of workers’ on-site operation technology, the vibrator does not vibrate enough, resulting in insufficient density of the cast body, excessive vibration and particle segregation, and it is easy to leave cavities when the vibrating spoon is pulled out. In addition, the vibrator is too noisy, affecting the construction environment. Self-flowing castables can automatically flow, flatten, compact and solidify without vibrating with a vibrator, avoiding the problems of vibrating castables. In order to meet the needs of the iron troughs of modern large blast furnaces, refractory manufacturers have developed self-flowing castables suitable for the iron troughs of large blast furnaces.
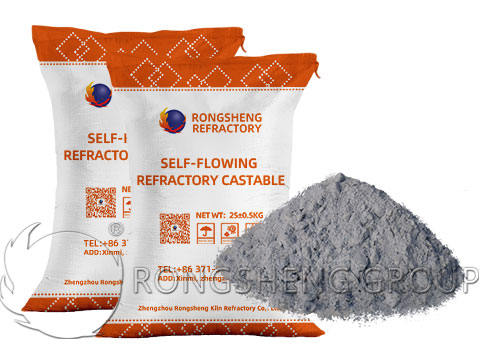
Application Advantages of Self-Flowing Castables
After France developed self-flowing castables, Japan studied self-flowing iron channel castables, which were developed based on low-cement and ultra-low-cement castables. It is a viscoplastic material with a low yield value and a certain plastic viscosity developed based on the principle of rheology. Its advantages are:
- (1) No vibration is required, and it can be automatically poured and compacted, greatly reducing labor intensity.
- (2) Compared with vibrating castables, the pore size is small and evenly distributed.
- (3) If the pumping process is used during construction, labor is reduced and work efficiency is improved.
- (4) It has stronger adaptability than vibrating castables and can be cast in any shape.
- (5) The performance is equivalent to or better than that of vibrating castables.
- (6) Reduce noise pollution.
- (7) It is easy to conduct construction performance tests on-site.
Therefore, the application of self-flowing castables has gradually become popular, and its scope is constantly expanding. Some people think that the performance of self-flowing castables is not as good as that of vibrating castables. It is outdated. By optimizing the particle size and matrix composition, self-flowing castables can be comparable to vibration castables of the same material in terms of water addition, density, and strength, and some properties are even better.
Factors Affecting the Fluidity of Self-Flowing Castables
There are many factors that affect the fluidity of self-flowing castables, mainly particle grading, water reducer, micro powder, cement type, and addition amount. They will be described below.
Effect of particle grading on the performance of self-flowing castables
The most famous and convenient stacking pattern in the field of refractory materials is the Andreassen distribution pattern. To obtain the best flow performance, an optimal stacking pattern is required. The Andreassen pattern basically solves this problem.
It is reported that when the particle composition is coarse particles (>1mm): 35%~50%; medium particles (1~0.045mm): 16%~30%; fine powder (<0.045mm): 23%~40%, vibration-free castables can be obtained. When the critical particle size is 8mm, the self-flowing castable can be obtained when its R (R=coarse particles/fine particles) is about 1.9. As the R value decreases, the self-flow value decreases significantly, and the viscosity of the castable increases. When the critical particle size is 5mm, the R value is between 1.5~1.85 to obtain self-flowing castables.
In addition, because self-flowing castables are developed based on rheological principles. It is a viscoplastic material with a low yield value and a certain plastic viscosity. Therefore, it requires a suitable particle size composition and an appropriate ratio of aggregate to matrix. As shown in the figure. When the particle composition is in zone 1, coarse and fine particle segregation will occur. When it is in zone 2, coarse particle collapse will occur. When it is in zones 3 and 4, a strong plastic state will occur. Only in zone 5 will it have self-flowing properties.
Effect of water reducer on the performance of self-flowing castables
Common water reducers include sodium hexametaphosphate, sodium tripolyphosphate, and high polymers. Different bonding systems should use appropriate water reducers. For example, sodium tripolyphosphate and sodium hexametaphosphate are more effective for silicon micropowder than for alumina micropowder. For silicon-free micropowder systems, high polymers are more effective as water reducers, and there are also quite strict requirements on the amount of water added.
Water reducer is a surfactant. The added inorganic and organic water reducers are both anionic. When dissolved in water, inorganic water reducers ionize anionic groups M and organic water reducers ionize anionic groups N. Since M is not a hydrophobic group, its surface activity is not significant, and it is mainly adsorbed on the surface of colloidal ions in the form of chemical adsorption. The organic anion group N is a hydrophobic group with strong surface activity, which is adsorbed on the surface of colloidal ions in the form of physical adsorption. A double electric layer is formed on the surface of cement and ultrafine powder particles, thereby changing the electromotive potential of the particle surface. Generate electrostatic repulsion between particles, so that cement ultrafine powder particles repel each other, disperse particles, and prevent the spontaneous formation of particle flocculation structure. And make the particles fully dispersed, homogenized and fill tiny gaps, release the water bound by the condensed particles, and fully wet the particle surface. It has a certain fluidity, and the macroscopic manifestation is that the rheological parameter shear stress of the slurry is reduced and the rheological properties are improved. In short, inorganic water reducers mainly rely on the electrostatic repulsion mechanism of changing and increasing the electromotive potential of the particle surface to achieve the purpose of dispersion. Organic water reducers mainly rely on the surface activity of organic water reducers to achieve the purpose of dispersion.
Effect of micropowder on the performance of self-flowing castables
1) Effect of silicon micropowder on self-flowing castables
Silicon micropowder has good rheological properties. When the same fluidity is achieved, as the amount of silica fume added increases, the amount of water added decreases, which enhances the filling property of the material, thereby increasing its volume density and reducing its apparent porosity. This is because there are a large number of ultrafine particles in SiO2 micropowder, which have a large specific surface area. In water, the surface of these particles is positively charged by adsorbing surfactants and has a certain zeta potential. The electrostatic repulsion between particles with the same charge causes the particles to disperse and form a uniform, low-viscosity slurry, which is dispersed between aggregate particles. It reduces the friction between aggregate particles, acts as a lubricant, and is conducive to improving the fluidity of the castable.
In ordinary castables, silicon micropowder becomes the first choice to obtain higher mechanical strength under the premise of lower water addition. The many chemical and physical properties of silicon micropowder directly affect the various properties of the castable. The higher the carbon content, the greater the pH value, and the construction time is drastically shortened. The higher the silica content, the better the construction performance when the pH value is around 7 and the carbon content is less than 0.5%.
When the same silicon powder is used, the mechanical strength at room temperature increases with the increase in the amount added, and the high-temperature flexural strength reaches the highest value at a certain value. After that, the flow value decreases with the increase in the amount added, the strength performance decreases, and the high-temperature performance also deteriorates. In particular, the linear change rate has a significant increasing trend.
Therefore, silica fume plays a good role in improving the construction performance of castables, but has an adverse effect on the strength after high-temperature firing.
2) Effect of alumina powder on the performance of self-flowing castables
In the Al2O3-SiO2 system, alumina powder is an indispensable filler. As a key parameter in the formulation, alumina powder affects the sintering degree and strength of the castable when determining the flow of the castable.
The literature points out that adding alumina powder with a moderate specific surface area and low Na2O content can obtain better flow properties. Of course, the additive system used for each alumina powder may be different.
Although alumina powder can promote sintering, it cannot be added too much because it can cause the castable to shrink significantly.
Both silicon powder and alumina powder have a filling effect on the capillaries, releasing the free water in them, increasing the solvent ratio of the system, weakening the thixotropic structure, and reducing the viscosity. When the amount of ultrafine powder added is small, there are a large number of capillaries, and the ultrafine powder mainly shows a filling effect. When the amount added is large, the capillaries are saturated and filled, and the ultrafine powder mainly shows a participating effect.
Effect of cement on the performance of self-flowing castables
The biggest influence of cement addition on the strength value of self-flowing castables is the strength value. As the amount of cement added increases, the drying strength also increases. For fluidity, it is not as sensitive as ultrafine powder and admixtures within a certain range. But relatively speaking, as the amount of cement added increases, its flow value tends to decrease.
In addition, the type and amount of cement added affect the initial setting time and final setting time. Therefore, the type and amount of cement added should be determined according to the construction conditions.
In addition to particle grading and particle shape, micro powder variety and addition, water reducer variety and addition, the factors affecting flow performance include cement fineness, activity and setting time, mixer type and mixing time, which all have an impact on self-flowing performance. This requires that, in the research and production of self-flowing castables, different measures should be taken according to the specific conditions of production and construction, and the best construction performance and use performance should be obtained through experiments.